PRODUCTS |  |
|
| Empty |  |
|
| | Air Quality/Purif. |  |
|
| | CO2 |  |
|
| | Damper Actuators |  |
|
| | DDC Controller |  |
|
| | Energy Detection |  |
|
| | Flow |  |
|
| | Gas Detection |  |
|
| | Humidity |  |
|
| | In-/Output Modules |  |
|
| | Light Control |  |
|
| | Motion Detection |  |
|
| | Occupancy |  |
|
| | Operator Terminal |  |
|
| | Power Controller |  |
|
| | Pressure |  |
|
| | BMS Smart Comm. |  |
|
| | Smoke/Fire/OVK |  |
|
| | Temperature |  |
|
| | Valves & Actuators |  |
|
| | Water Detection |  |
|
| | Weather Station |  |
|
| | Wireless |  |
|
| | Zone Controller |  |
|
| |
|
|
GASDETEKTERING - HEXANE, C6H14 |
|
 |
|
|
Hexane is a saturated, acyclic
hydrocarbon with the formula C6H14,
with 5 different structural isomers.
These isomers are all liquids at room
temperature and has fairly similar physical properties (melting
point, boiling point, specific heat, etc.).
Hexane is present to some degree in gasoline.
Basics on gas monotoring
Harmful Gas
Gas monitoring of combustible gases serve to obtain alarm in case of
gas leakage. Pentane is a heavy explosive gas
with a flammable range from 1.2 to 7.4 vol%.
The density of the gas is 2,79. (Air = 1,0)
The detector should be mounted appr.
0.2 m above the floor.
The weight of the gas allows it to accumulate in deep points both
indoors and outdoors. Appropriate alarm levels
can be determined from case to case, but outdoors, we recommend
level 1 to 10% of LEL and level 2 to 20% of LEL.
Information
on LEL och explosion hazard
Alarm level 1 should result in control measures while alarm level 2 should be regarded as an emergency alarm.
When forwarding alarms to local emergency services, we recommend
using two detectors at alarm level 2 in order to avoid false alarms.
Alarm level 2 should result in flashlight and/or siren/gas alarm
plate.
Flashlight should be used for alarm level 1.
Outdoor Gas Monitoring
Since recommendations on monitoring always depend on the
circumstances in the various specific cases, one must always
evaluate the effects of gas monitoring. For
detector placement consider the following:
-
All deep areas adjacent to storage tanks,
pumps, valves, vaporizers must be investigated. Monotoring
should take place if accumulation risks in case of leakage are
considered great.
-
Placement of detectors at potential leak
areas, like tank valves should be considered. It is important to
consider the effects of weather and wind on the gasflow.
Plants have sometimes been built so that not
even strong winds could have prevented a certain accumulation of
flammable gas around the alarm object.
The advantage of creating a special alarm area is that alarms
from the gas monitoring unit can be obtained at a very early stage.
The disadvantage of creating a special
alarm area is that explosive gas concentrations can build up in here.
With no special alarm area, explosive gas concentrations might not
develop.
Choice of Equipment
The Stand-alone detector is a detector
where power supply, alarm and control functions are integrated in
the detector housing. This detector is used where very simple
systems are sought and only few monitoring points are desired
|
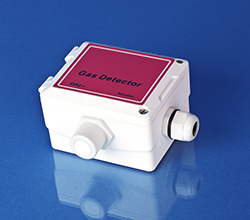
Analog detector AHEX,
Wall |
|
|
|
CE |
Environm. |
AHEX |
|
|
 |
 |
 |
|
|
declaration |
declaration |
Datasheet |
|
|
|
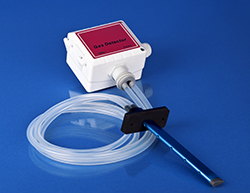
Analog detector AHEX, Duct |
|
Duct |
IP |
|
Calibr. |
|
 |
 |
 |
 |
|
Kit |
Protection |
Manual |
Certificate |
|
|
|
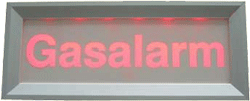
Gas alarm plate for gas detector
|
|
|
|
|
|
|
|
|
 |
|
|
|
|
Datasheet |
|
|
|
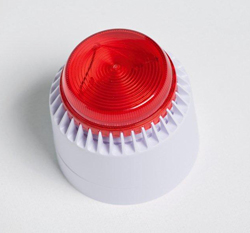
OAW 24
Combined warning horn/flashlight
for
gas detectors |
|
|
|
|
|
|
|
|
 |
|
|
|
|
Datasheet |
|
|
|
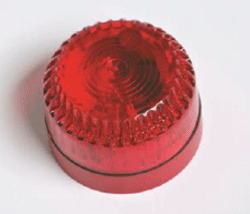
OA 24
Flashlight |
|
|
|
|
|
|
|
|
|
 |
|
|
|
|
Datasheet |
|
|
|
|
|
|
|
The multipoint system equipped with an
instrument for gas monitoring is based on detectors providing a
gas leak unit with a signal related to the gas concentration.
The signal is then processed in the gas leak unit where measurements,
alarms and control functions are obtained. The
most common gas leak unit is of this type and the CGD model is used
for several measuring points.
More here
Preferred system functions
Regardless of the type of gas leak unit you choose, we suggest a
study of the following features:
ALarm: |
Should the
facility have one or two alarm levels per detector? |
Control signals: |
Should the facility have
one relay per alarm level and sensor?
Should the relay have a function for time delay?
Should the facility have computer output? |
Measurem.
values: |
Should it be possible to
read alarm values?
Should it be a digital, an analog or a flashing sign for
gas alarm? |
Diagnostics: |
Should the facility itself
be able to identify sensor errors, open circuits and
instrument errors? |
Safety: |
Should the plant be
equipped with a battery backup? |
The exchangeable sensor X-CHANGE turns the
recalibration into a home game:
-
Delivery of recalibrated sensor
cartridges
-
Easy exchange, no specialized company
needs to come to you
-
Available for every gas type
-
At guaranteed exchange prices
-
Increased reliability (SIL2-software)
-
Important time and cost savings
The X-Change support guarantees a price based
on the consumption of the sensor capacitance.
For each uncalibrated sensor returned to AP,
you will receive a credit for the unused capacity of the sensor.
More >
Legal and safety requirements
The devices are manufactured
according to the regulations and various directives such as EN 50545, etc.
Products delivered by AP meet and even exceed the new European Standard EN
50545.
The safety features check the connected
warning devices on functionality and open circuit day and night (Level
SIL2 according to EN 50271).
|
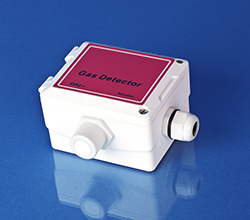
Field Bus detector, BHEX - Wall
Modbus, BacNet, etc.
|
|
CE |
to do |
|
BHEX |
|
 |
 |
|
 |
|
declaration |
Manual |
|
Datasheet |
|
|
|
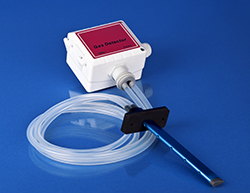
Fieldbus detector, BHEX - Duct
Modbus, BacNet, etc.
|
IP |
Calibr. |
Underst. |
Art & |
|
 |
 |
 |
 |
|
Protection |
certificate |
RS485 |
Science |
|
|
|
|
|
|
|
|
Environm. |
Duct |
|
|
|
 |
 |
|
|
|
declaration |
Kit |
|
|
|
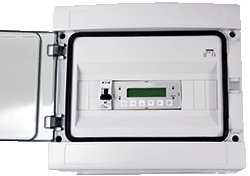
Gas Leak Unit, CGD |
Gas Leak Unit |
|
|
Quick and easy replacement of sensor |
|
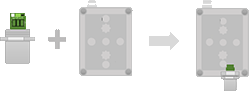 |
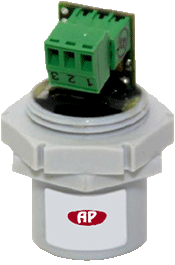 |
|
|
-
Open the housing with a screwdriver.
-
Disconnect the sensor cable and unscrew
the disused sensor head.
-
Exchange the sensor cartridge (3) and
connect the cable of the new sensor head to the PCB.
-
Close cover of the housing with the
screws (1). The recalibrated sensor is ready for use at once.
|
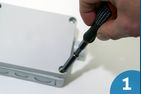 |
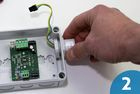 |
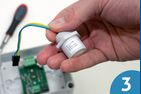 |
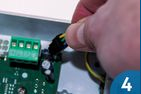 |
|
|
|
|
|
Electrical products in an explosive environment
A small amount of energy - a flame, spark, high surface temperature
or similar is required to ignite an explosive gas mixture.
Products installed in an area with a potential explosion hazard must
of course in themselves not be a potential explosion hazard.
For this reason, the products are manufactured in such a way that
this cannot occur.
The equipment must also be labeled and tested - ATEX classified - by
the approved testing authority.
The Ex-class information is available in "Swedish Standard"
The choice of which Ex-classification is required is determined
by factors such as type of gas, permissible maximum surface
temperature and potential explosive hazards in the area where the
products are to be installed.
The potential explosion hazard in the different areas is determined
by the zone classification according to "Swedish Standard".
More about ATEX-products can be found in the following link
ATEX explosionproof detectors
|
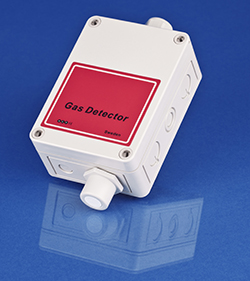
Combi
detector CHEX - Wall
ModBus, Analog, Relay Output
|
CE |
Art/Science |
Underst. |
CHEX |
|
 |
 |
 |
 |
|
declaration |
RS485 |
RS485 |
Datasheet |
|
|
|
|
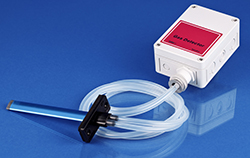
Combi
detector CHEX - Duct
ModBus, Analog, Relay Output |
Environm. |
Calibr. |
CE |
missing |
|
 |
 |
 |
|
|
declaration |
certificate |
deklaration |
Manual |
|
|
|
|
|
|
|
|
|
Duct |
|
|
|
|
 |
|
|
|
|
Kit |
|
|
|
|
|
|
|
|